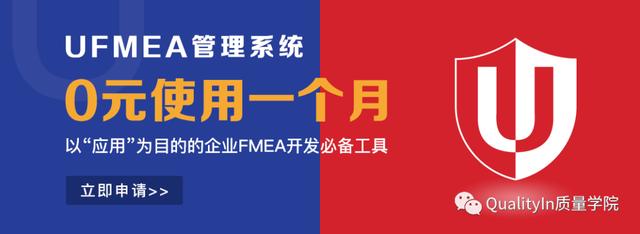
前言
沒有衡量就沒有增長,同樣,中國智造如果沒有可衡量、可實(shí)現(xiàn)的指標(biāo)體系,也終將淪為一句口號。工業(yè)體系不缺乏指標(biāo),然而,要想找到關(guān)鍵指標(biāo)并搭建起能夠行之有效的指標(biāo)體系并非易事。
據(jù)了解,在各種類型的指標(biāo)體系中,普遍采用的指標(biāo)大概也就幾十個。無論哪種指標(biāo)體系,OEE指標(biāo)都是一個難以忽視的重點(diǎn)。因?yàn)镺EE就是定義世界一流制造企業(yè)的核心指標(biāo)。
OEE(Overall Equipment Effectiveness)是一個獨(dú)立的測量工具,它用來表現(xiàn)實(shí)際的生產(chǎn)能力相對于理論產(chǎn)能的比率。
設(shè)備綜合效率OEE的計算公式,可以寫作“時間開動率*性能開動率*合格品率”,也可以寫作“(合格產(chǎn)量*理論加工周期)/負(fù)荷時間”,或者寫作“合格產(chǎn)品的理論加工總時間/負(fù)荷時間”。
OEE本質(zhì)是設(shè)備負(fù)荷時間內(nèi)實(shí)際產(chǎn)量與理論產(chǎn)量的比值,也是對周期內(nèi)用于加工的理論時間和負(fù)荷時間的百分比的計算。它反映的是企業(yè)/產(chǎn)線的實(shí)際生產(chǎn)能力,因此OEE是諸多工業(yè)指標(biāo)中的核心關(guān)鍵指標(biāo)。
雖然OEE的計算公式看起來很簡單,實(shí)際上它的每一個計算因子都需要被層層分解。比如,時間開動率被分解為“開動時間/負(fù)荷時間”,而負(fù)荷時間又被分解為“日歷工作時間-計劃停機(jī)時間”……
同時,由于工業(yè)生產(chǎn)環(huán)境復(fù)雜,OEE的計算也需要考慮到各種因素,其計算方式也會因場景不同而不同。比如,工廠停水、停電、停氣造成的設(shè)備無法工作,以及等待訂單、等待檢查、等待上一道工序這些情況,到底應(yīng)該如何歸屬和計算,因?yàn)闅w屬和計算方式的不同都會造成OEE計算結(jié)果的巨大差異。

也正因?yàn)镺EE具有明顯的場景、行業(yè)屬性,我們在看待OEE的計算結(jié)果的時候,不能一概而論。你或許聽過“OEE分?jǐn)?shù)超過85%就達(dá)到了世界一流工廠的水平”這種說法,這還要從OEE這個指標(biāo)的歷史淵源說起。
首先是這個概念的時代背景是上世紀(jì)70年代,地點(diǎn)是日本,行業(yè)是汽車制造。當(dāng)時日本工廠維護(hù)研究所的中島誠一首次引入了世界一流OEE分?jǐn)?shù)的說法,因?yàn)樗l(fā)現(xiàn)日本授予的杰出工廠獎獲得者其OEE分?jǐn)?shù)均超過了85%。

雖然世界一流OEE分?jǐn)?shù)的說法最初是用于汽車制造行業(yè),但并不妨礙它擴(kuò)展到整個離散制造領(lǐng)域。目前在離散制造行業(yè)已經(jīng)公認(rèn)“85%”這種說法,它也是眾多離散制造企業(yè)奮斗的目標(biāo)。
因?yàn)椋壳皝砜创蟛糠值脑擃I(lǐng)域企業(yè)的OEE分?jǐn)?shù)普遍在60%,甚至低于40%的企業(yè)也不在少數(shù)?!?00%(完美)”、“85%(世界一流)”、“60%(一般)”和“40%(低水平)”這四個OEE分?jǐn)?shù)檔次已經(jīng)成為行業(yè)基準(zhǔn)。

當(dāng)然,OEE的分?jǐn)?shù)并不僅僅是一個數(shù)字,不是因?yàn)樗枰獜?fù)雜的分解才能計算得出,而是這些數(shù)字背后切實(shí)的反應(yīng)了工廠和產(chǎn)線非常具體的“失分點(diǎn)”。
從整個生產(chǎn)過程來講,OEE的損失可以歸納為以下三個因素:可用性損失、性能損失、質(zhì)量損失。這些損失還可以細(xì)化為“設(shè)備六大損失”:機(jī)器故障、速度下降、停頓、調(diào)整與設(shè)置、啟動損失、缺陷與返工。追蹤、優(yōu)化OEE的一個重要目的就是減少制造業(yè)所存在的設(shè)備六大損失。
接下來,分享完整版OEE培訓(xùn)教材,歡迎收藏學(xué)習(xí)!
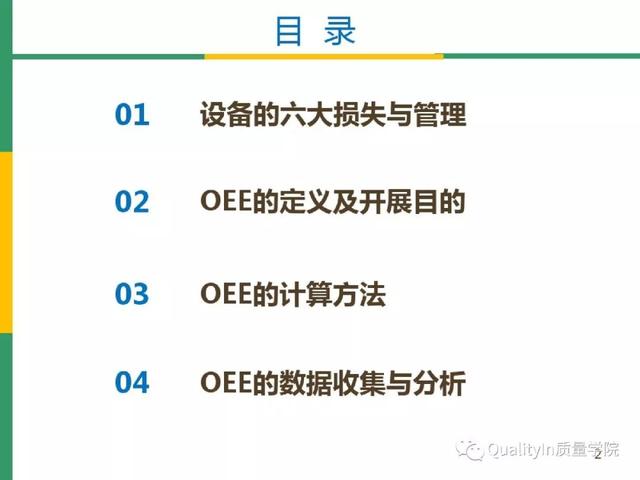


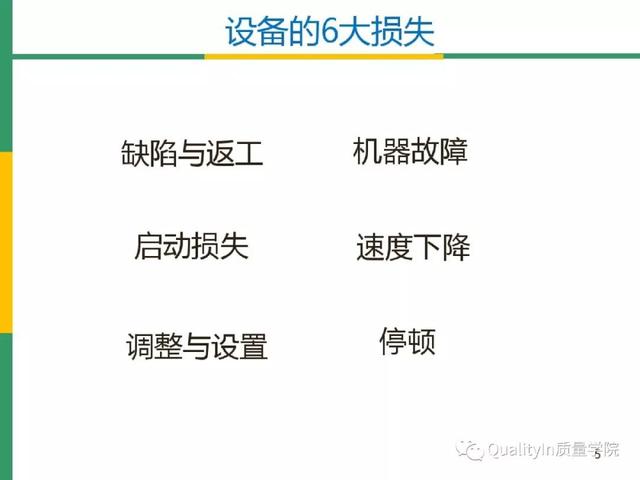



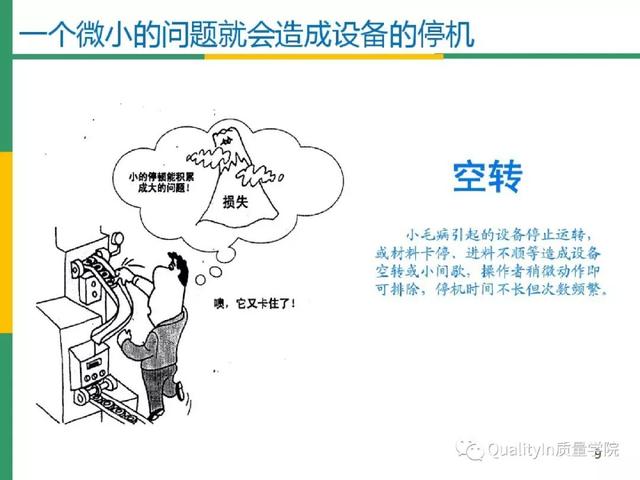

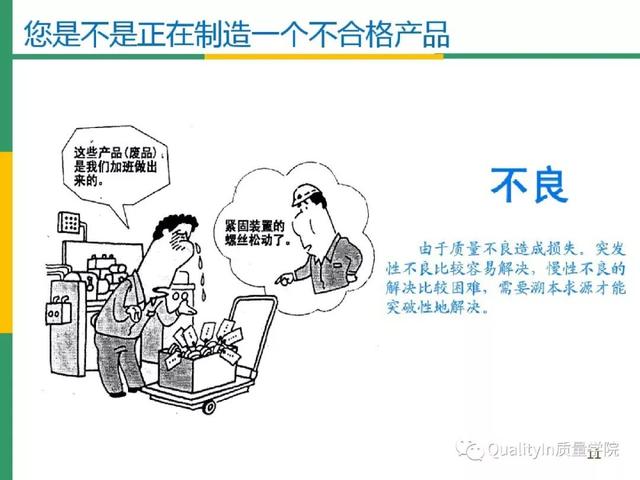







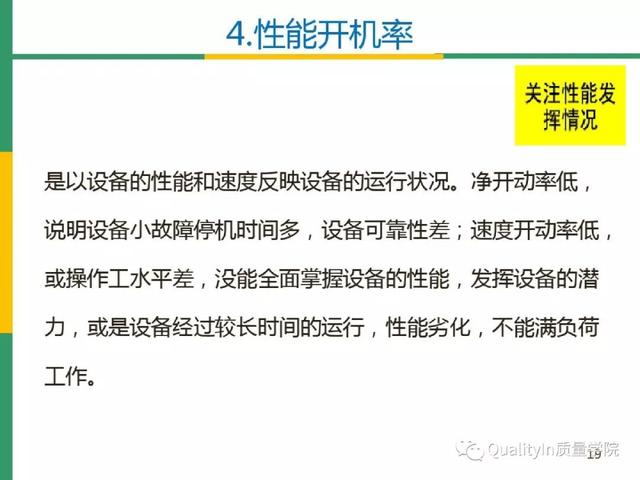



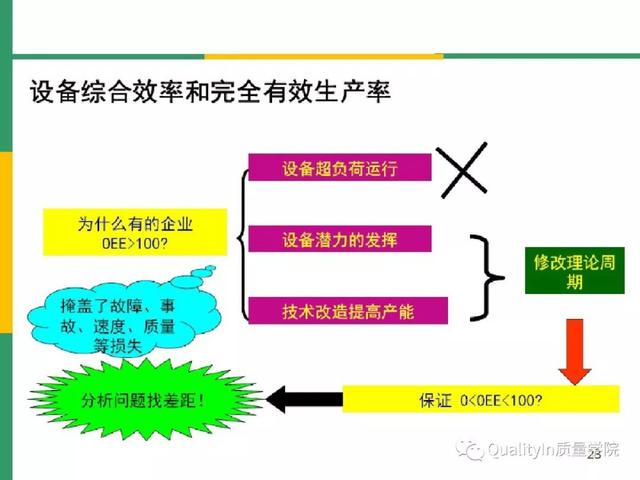


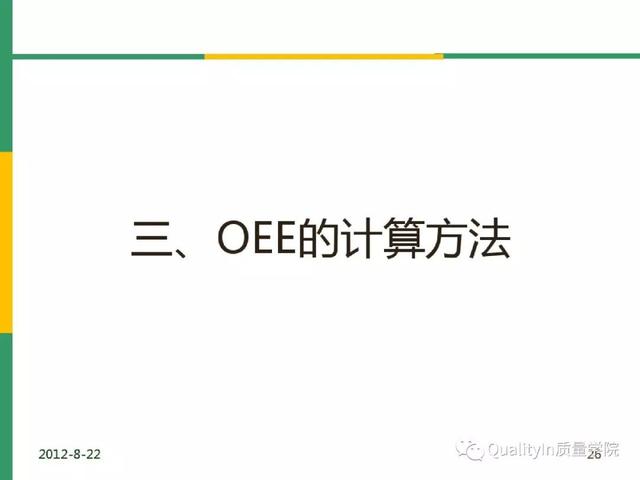
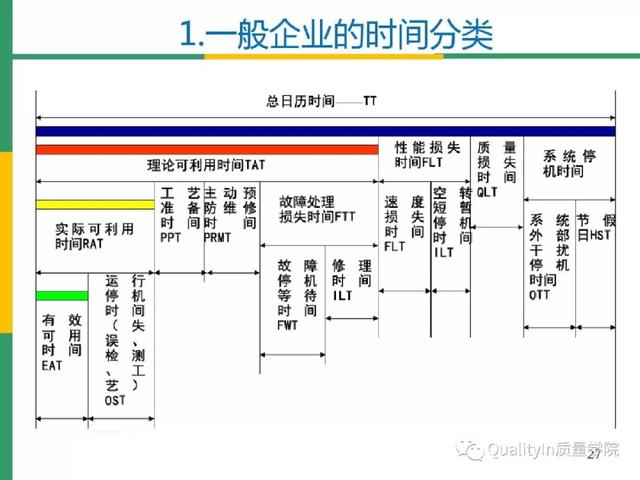
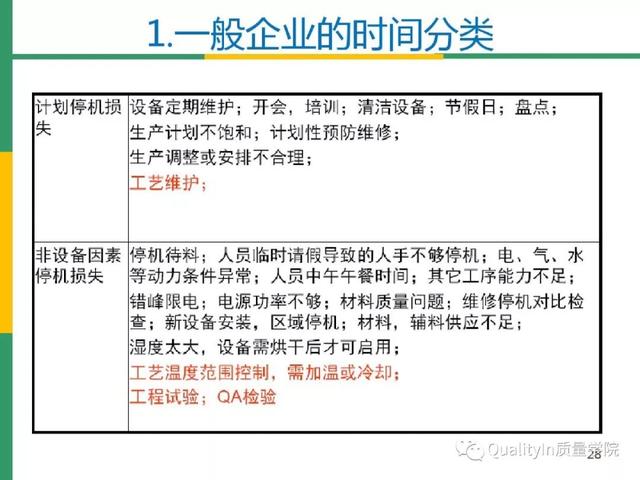

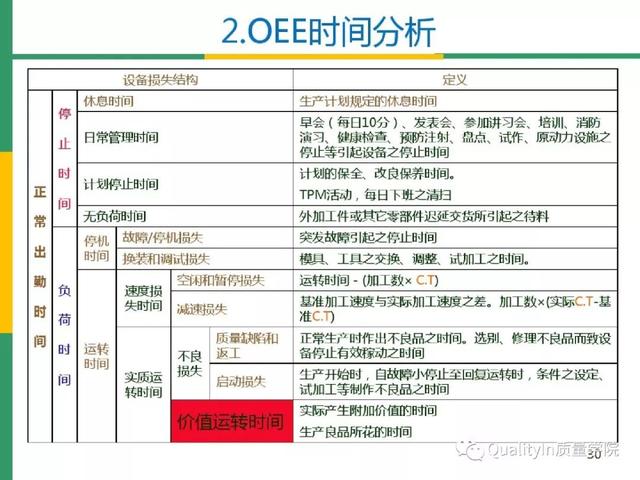
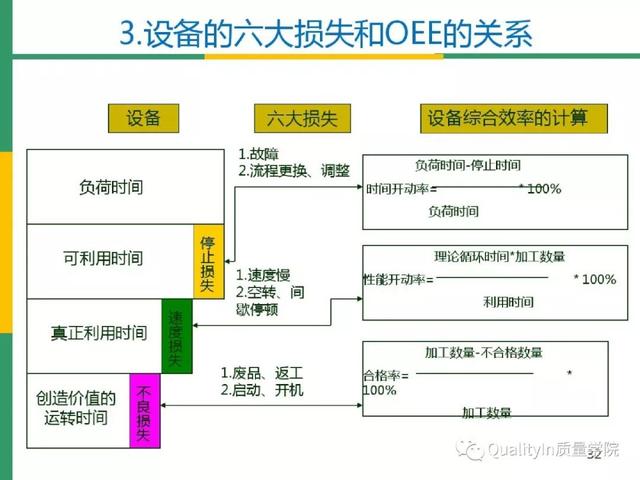

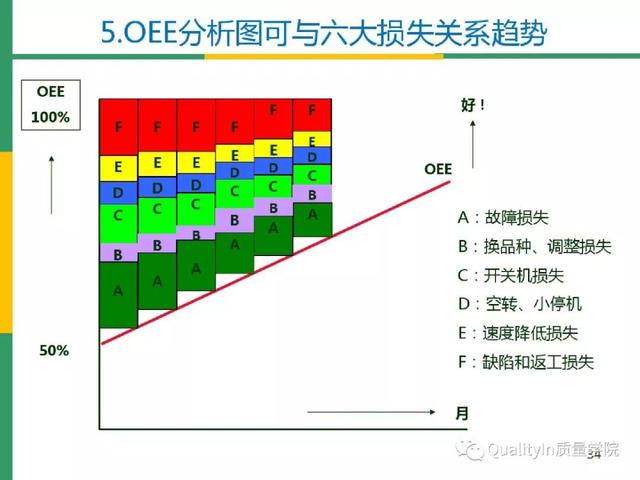

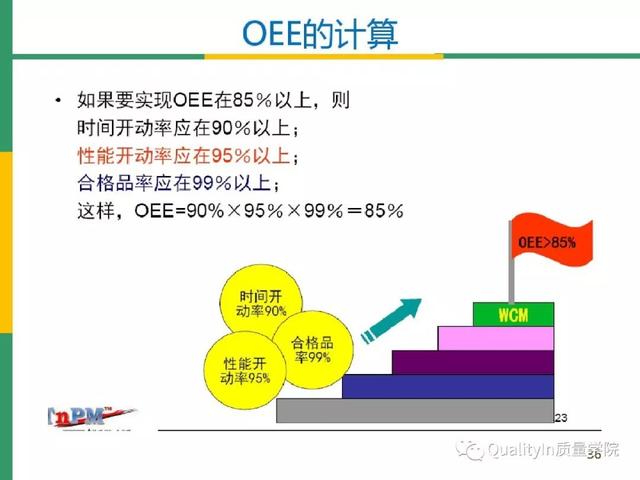







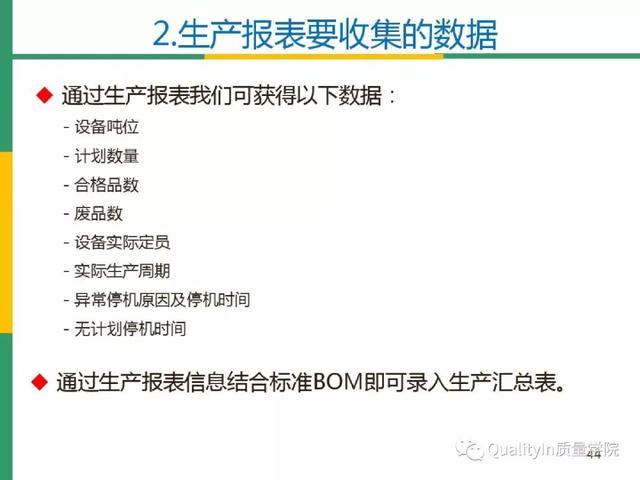



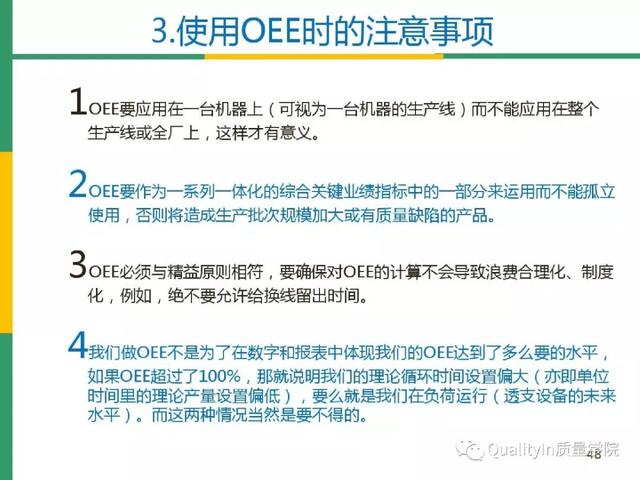
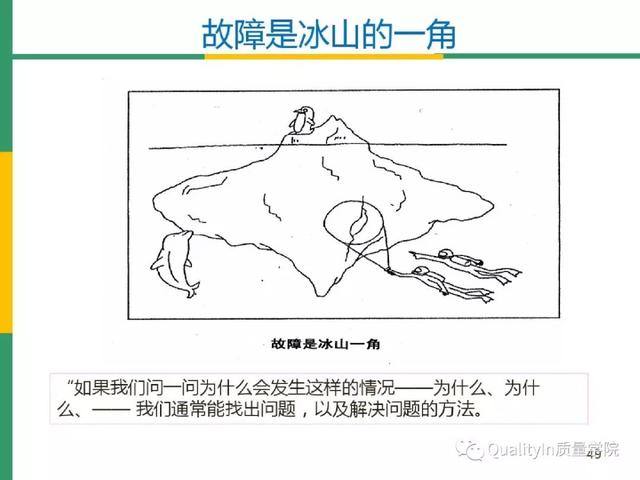

更多專業(yè)質(zhì)量文章,請?jiān)L問QualityIn質(zhì)量學(xué)院官網(wǎng)。
好了,這篇文章的內(nèi)容發(fā)貨聯(lián)盟就和大家分享到這里,如果大家網(wǎng)絡(luò)推廣引流創(chuàng)業(yè)感興趣,可以添加微信:80709525 備注:發(fā)貨聯(lián)盟引流學(xué)習(xí); 我拉你進(jìn)直播課程學(xué)習(xí)群,每周135晚上都是有實(shí)戰(zhàn)干貨的推廣引流技術(shù)課程免費(fèi)分享!